前回は研磨について記事を書きましたので、今回は研磨の中でも特に多層配線形成において行われるCMPという研磨法についてまとめました。
目次
配線形成工程
半導体製造プロセスはIC(集積回路)の出来るまでの前工程と、ICチップをパッケージにして製品として組み立てる後工程の2つに分けられます。
多層配線形成は前工程のほぼ最終の段階です。
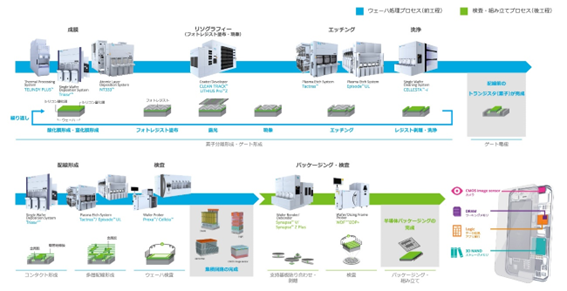
多層配線と平坦化
LSIと多層配線
シリコン等でできた一つの半導体基板(ウェーハ)の上にトランジスタ、抵抗、コンデンサ、ダイオードなどの回路素子を載せた電子回路のことを集積回路(Integrated Circuit ; IC)といいます。これを通常は大きさ数mm~10数mm角のICチップに切り出して、一つずつパッケージに入れて扱います。
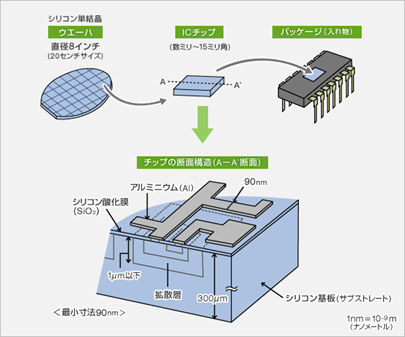
このような集積回路の中でも、一つのチップに集積される素子の数が1,000個~数百万個にのぼるものをLSI(Large Scale Integrated circuit)と呼びます。
素子が非常に多いことから複雑な機能を実現できるのが特徴で、自動車、テレビ、スマートフォンなど私たちの生活に密接に関係する多くの電子機器に使われています。
電子回路では素子同士を配線によって接続する必要がありますが、LSIでは万単位の素子を相互に接続するため、必要な配線の本数も増え、レイアウトも複雑化します。
そのため、一つの平面にすべての配線を作ろうとすると、つなぎたい素子と素子の間に別の素子が存在する場合はそれを迂回せねばならず配線が長くなったり、場合によっては接続できなくなったりすることがあります。
そこで、配線をマンションのように階層構造にして積み上げるということを考えたのが多層配線です。
各素子を相互に接続する金属配線層が複数層になるものを多層配線(multi-level interconnection)と言います。
配線の層数が増すと製造工程は複雑になりますが、先述のような単層構造における配線の問題を解消し、LSIチップのサイズを小さくしたり性能を向上させたりすることが可能になります。
Al配線からCu配線へ
LSIの配線には当初Alが使われており、その歴史は20年近く続きました。
Alは加工性に優れ、軽量・低コストであるというメリットがあります。
しかし、半導体製造プロセスの微細化が進むにつれて、従来のAl配線では配線遅延の問題が出てきました。
配線遅延とは信号が配線を伝わる時間の遅れのことで、電気抵抗が主な原因となります。配線遅延が生じるとLSIの処理能力に影響が出てしまいます。
電気が流れるということは電子が移動するということですので、結晶中に自由電子を多数もつ金属は電気を通すことができます。このような電気の流れ(電子の移動)を妨げるものが電気抵抗です。
電気抵抗の原因として考えられているのが格子振動というものです。格子振動は結晶を構成する原子・イオンが特定の位置関係を持ったまま熱エネルギーによって振動することを指します。
金属の格子は金属イオンによって正に帯電しています。この格子が熱運動で揺れ動くと、負に帯電している電子はクーロン力の影響を受けて自由な動きが妨げられ、電気抵抗が生じるのです。
金属のうち最も抵抗率の小さい物質は銀(Ag)で、次に銅(Cu)、金(Au)、アルミニウム(Al)と続きます。
CuはAlに比べて加工性が劣りますが、Agに次いで電気抵抗が小さいため、細い配線にしても電気がスムーズに流れます。
どうせなら一番抵抗の小さいAgにすればよいのでは?と思うかもしれませんが、そこはコストの問題で、価格の安いCuに軍配が上がります。
主な導電材料の特性をまとめた以下の表を見ると、それぞれにメリット・デメリットがあることが分かると思います。
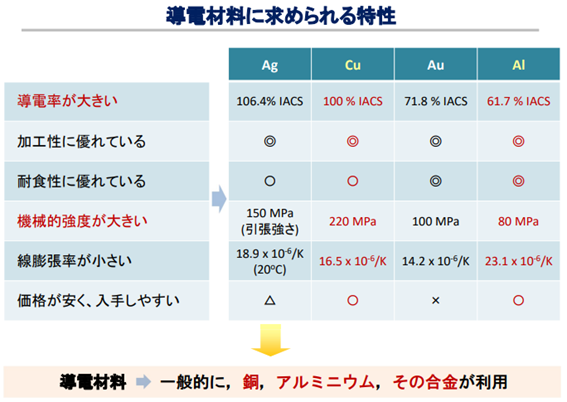
またAl配線の場合に生じる問題として、エレクトロマイグレーションというものもあります。
エレクトロマイグレーションとは、電流が高密度で流れた場合に、金属配線に流れる電子が金属イオンと衝突し、金属イオンを押し動かす現象です。
通常、電子は非常に小さいため金属イオンの格子の間をほとんど衝突せずに移動します。
しかし、細い配線内を高密度の電流が流れると自由電子と金属イオンの衝突が起こりやすくなります。
この現象によって金属原子が減少する箇所はボイド(空洞)となって断線し、金属原子が堆積する箇所はヒロックと呼ばれる丘状の突起物となって隣の配線と短絡する(ショート)という恐れがあります。
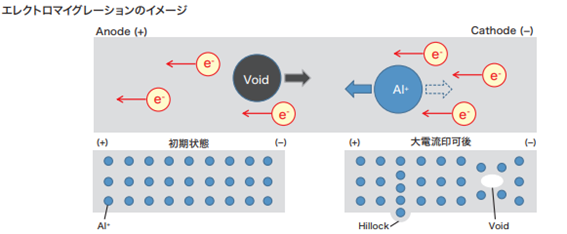
Cuは電気抵抗が小さいことに加え、Alと比べて上記のエレクトロマイグレーションを起こしにくいというメリットもあり、今ではAlに代わる配線材料として用いられるようになりました。
銅ダマシンめっき
このようにCuはAlの欠点を補う形で配線の材料として選択されるようになりましたが課題もありました。
従来のAl配線はプラズマエッチングによってAlを配線の形に直接加工し、その上からSiO2などの絶縁膜材料を埋め込んでいました。
しかし、CuはAlと比べて加工性に劣るため、従来のようなプラズマエッチングによるパターニングで微細化の要求に対応した複雑な配線に加工するのは困難だったのです。
このような状況を解決したのが、IBM社が1990年代後半に開発したダマシン法と呼ばれるめっき技術です。
ダマシンとは、ある素材に異種の素材を埋め込む技法である「象嵌」の意味です。
ダマシン法は次のような工程で行われます。
- SiO2など絶縁膜の層にエッチングで溝を作る。
- 電解めっきでその上にCu の膜をつける。
- CMP装置で上部のCuを削り取る。
- SiO2層の溝の中にあるCuだけが残って配線ができあがる。
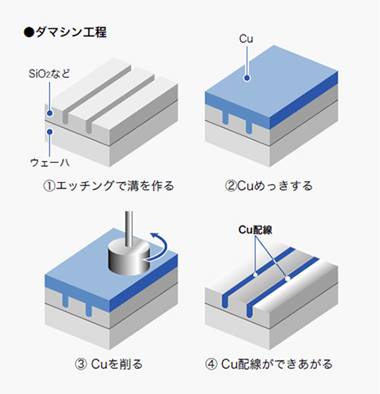
溝の部分をCuめっきで埋めることで配線が形成されるため、その特徴をとらえてダマシン(象嵌)と呼ばれます。
めっきの原理は電気分解で、Cu材料を陽極に、めっきを施したい部分を陰極にもってきて電圧をかけることで、陽極側ではCu → Cu2+ + 2e– の反応が起きてCuが溶けだし、陰極側では反対にCu2+ + 2e– → Cuの反応が起きて、陽極で溶けだしたCuが再び析出してめっきを作ります。
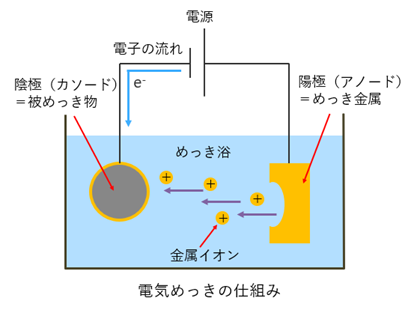
従来のAl配線の工程と比べると以下のようになります。
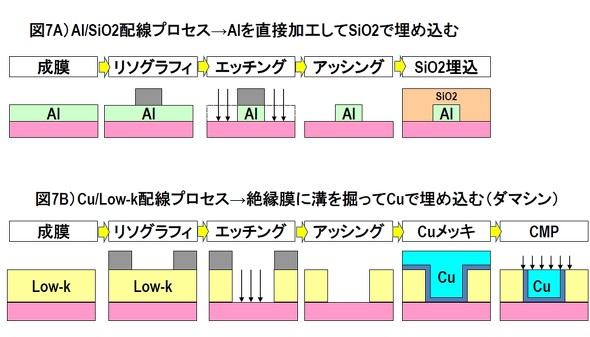
CMPとは
CMPとは、Chemical Mechanical Polishing(化学的機械的研磨)の頭文字を取ったもので、名前の通り、化学的研磨と機械的研磨を組み合わせた研磨方法です。
多層配線ではいくつもの配線層を積み重ねていくため、上面が平坦になっていないとその上に作られる次の層もゆがんでしまい、下図の左側のようになってしまいます。
そのためダマシン法ではCMPによる平坦化が必須となります。
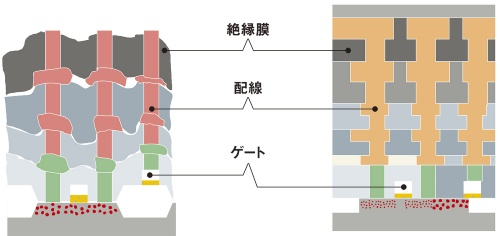
CMPでは砥粒と薬品を混ぜ合わせたスラリーという研磨用の液体と研磨パッドとを使って加工物表面を研磨します。
機械的研磨とは、砥粒を使って物理的に加工物を研磨する方法です。
砥粒としては主に、アルミナ(Al2O3)やシリカ(SiO2)などの無機粒子が使われます。
スラリーにつかわれる薬品
化学的研磨とは、化学反応により表面層を軟化させて特定の材料を優先的に除去する方法です。
化学的研磨に寄与する材料として、研磨スラリーには以下のものが含まれます。
・酸化剤
・錯形成剤
・防食剤
・pH調整剤
これらの化学的研磨に関係する成分がそれぞれどのように働くのか見ていきましょう。
酸化剤
CMPでは研磨の際にCu表面を酸化して脆弱な膜にすることで機械的研磨を容易にします。
Cu表面を脆弱な膜にするためには水溶性の錯体を形成する必要があるのですが(次の錯形成剤の項で説明します)、錯体を形成するためにはまずCu 表面を酸化させてCuの水和物イオンを形成する必要があります。
つまり次のような反応を起こさせます。
Cu → Cu2+ + 2e–
Cuはイオン化傾向が比較的小さい金属であるため、上記の酸化反応を進行させて水和物イオンを形成するためには酸化剤が必要となります。
CMPプロセスでよく用いられるのは過酸化水素水です。
過酸化水素水は次のような反応で自身は還元され、相手を参加するため酸化剤として働くのです。
H2O2 + 2H + 2e– → 2H2O
錯形成剤
酸化剤によって生じたCuイオンはスラリーに可溶な錯体を作ることで効率よく除去できるようになります。
Cuは一般にアルカリに対して耐食性がありますが、アンモニアやアミンとは錯イオンを形成して溶解します。そのため、錯形成剤としてはグリシンやクエン酸などのアミノ酸、アンモニアなどのアミン類が用いられます。
スラリーに可溶な錯体ができた状態で砥粒を加えて研磨パッドでCu表面を研磨すると、凸部が除去しやすくなります。
除去した錯体層の下には新しいCu表面が現れますが、再度スラリーによって錯体が形成されて除去されます。
これが繰り返されてCu の研磨と表面の平坦化が行われます。
錯形成剤によって錯体が形成される反応について、アミン類の代表としてアンモニアの場合、アミノ酸の代表としてグリシンの場合をそれぞれ見ていきましょう。
アンモニアの場合
アミンとは下図の一般式で表されるように、アンモニアNH3の水素原子を炭化水素基Rで置換した化合物の総称です。
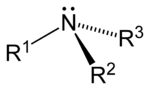
H原子が炭化水素基で置換された数によって、1個のH原子が置換されたものを第1級アミン、2個の場合を第2級アミン、3個の場合を第3級アミンといいます。
3つのRすべてがHであるアンモニアもアミンに含まれます。
アミンの大きな特徴として、N原子がローンペア(非共有電子対)を持つ、ということが挙げられます。
余っているローンペアを他の原子に与えたがっている状態なので、電子供与性を持ちます。
一方が電子対を与えることによる結合といえば配位結合です。
アンモニアはCuに電子対を与えて配位結合し、錯体を形成します。
下図はアンモニアとの錯体(テトラアンミン銅(Ⅱ)イオン、[Cu(NH3)4]2+)です。
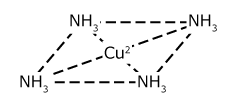
この錯イオンが形成されることでCuは水溶性となり、スラリーに溶かして除去しやすくなります。
グリシンの場合
アミノ酸の例としてはグリシンが挙げられます。
アミノ酸は一般に、分子内にアミノ基とカルボキシル基の両方を持つ有機化合物を指します。
中でも中心となる炭素に-NH2、-COOH、-H、-Rの4種類がついたものをαアミノ酸といいますが、その中のR=Hのものがグリシンです。
グリシンはαアミノ酸の中で最も分子量が小さく、不斉炭素を持たない唯一のαアミノ酸です。
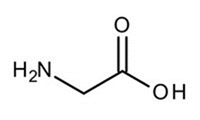
アミノ酸にはアミノ基が含まれますので、やはりアミンと同様にローンペアを使って配位結合し、錯体を形成します。
グリシンはCu 水和物イオンと水溶性の4配位のキレート錯体を形成することが知られています。
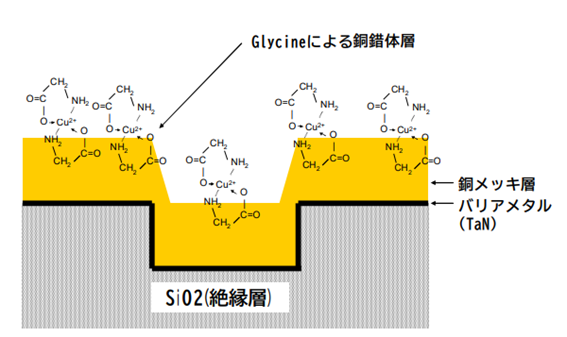
防食剤
これまではあえて腐食が起こりやすい状態を作るプロセスを見てきましたが、使用する薬品や研磨の強さによっては、絶縁膜よりも金属膜やそのエリア一帯が深く研磨・腐食されてしまう現象が生じます。
これらの現象はエロージョン・コロージョン、ディッシングと呼ばれます。
CMPの目的は絶縁膜を削ることなく金属層のみを研磨することです。
つまり下図でいうと、(a)の状態から(b)の状態にするのが目的です。
しかし、研磨が行き過ぎると絶縁膜も削られてしまい、エロージョン・コロージョンやディッシングが生じた(c)のような状態になってしまうのです。
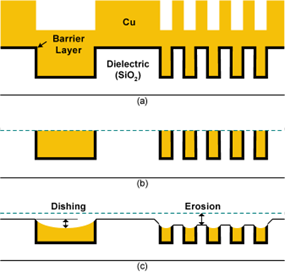
ディッシングとは、Cu配線が過剰に研磨されて皿のようにくぼんでしまう減少を指します。エロージョン・コロージョンは微細配線が緻密に配列した箇所の絶縁膜が過剰に研磨されてしまう現象を指します。
エロージョン・コロージョンのうち、エロージョン(erosion)は日本語で「浸食」と呼ばれ、機械的に起こる磨耗作用のことです。コロージョン(corrosion)は「腐食」と呼ばれ、電気化学的作用によって生じる変質を指します。
このような研磨中・研磨後におけるCuの腐食・浸食を防ぐために使われるのが防食剤です。
防食剤の成分としては、主にベンゾトリアゾール(BTA)という下図の化合物が使われます。
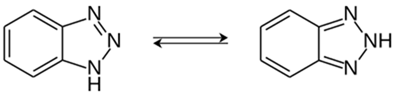
先ほど見たアミンやアミノ酸はスラリー可溶な錯体を形成しましたが、BTAの場合は反対に、スラリーに不溶な錯体を形成します。
この錯体は分子同士が鎖状につながって伸びていくため、Cu層の上に下図のような皮膜ができます。
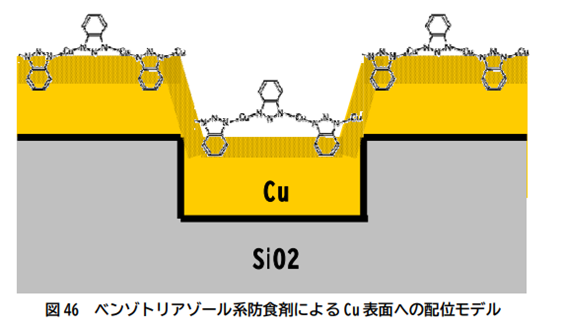
Cu-BTA錯体が作る皮膜は配線保護層となり、配線部に研磨パッドが接触することで生じる浸食と研磨スラリーによる腐食からCu配線を保護します。
pH調整剤
pH調整剤は研磨速度の最適化、砥粒の安定性向上といった役割があります。
アンモニアや水酸化カリウムなどが用いられます。
プールベ図
pH変化とCuの腐食しやすさを判断するためにプールべ図というものが使われます。
プールベ図は、電位-pH図とも呼ばれ、横軸がpH、縦軸が酸化還元電位を表した下のような図です。

酸化還元電位(ORP;Oxidation Reduction Potential)とは、酸化させる力と還元させる力の差を電位差(E0)で表した数値のことです。
標準状態での水素電極の電位を0と定義し、この基準との差で表されます。
この値がプラスで大きければ酸化力が強く、マイナスで大きければ還元力が強いということになります。
イオン化傾向に概ね一致しますが、イオンの濃度、錯体の形成、pH、などの要素によってイオン化列の通りにならない場合も出てきます。
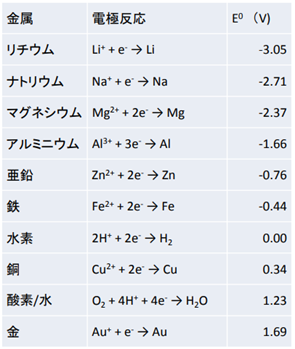
プールべ図を見ると次のような領域があることがわかります。
不活態域: 電位が低く、金属状態で安定している領域。腐食はほとんど生じない。
腐食域: 溶液中のイオン状態が安定な領域。腐食が起こりやすい。
不動態域: 表面に酸化物の膜を形成する領域。腐食は抑制される。
つまり、プールべ図を見るとどのpH領域であればCuが腐食しやすく研磨速度を高速化できるか、ということが判断できます。
研磨プロセスでは表面粗さを極限まで抑えて滑らかにするとともに、いかに素早く処理するかということも課題になるため、最適なpH領域を見出すことが重要になるのです。
参考)
・橋口 裕一「化学的機械的研磨(CMP)用スラリーにおける電気化学」 Electrochemistry Vol.74,No. 12, 2006
・佐藤 淳一「よくわかる半導体プロセスの基本と仕組み」 ㈱秀和システム, 2020
・前田 和夫「はじめての半導体プロセス」技術評論社, 2011
・三木 武、西 亜紀子「表面分析によるCu-CMP工程の評価」 SCAS NEWS, 2001-Ⅱ(㈱住化分析センター 技術広報誌)
・大塚 俊明「金属腐食理解のための電位-pH図の利用とその限界」表面技術 Vol.64, No.2, 2013
・中村 友二「LSIの配線技術と表面科学」表面科学 Vol. 35, No. 5, 2014
8/21(水)学習時間:5.25H
・橋本の物理(2)(3)
・3021 トライアルと偏差値
・3014 トライアルのタイミングと上位合格
8/22(木)学習時間:5H
・橋本の物理(4)(5)
・ダマシンめっきについて
・0038 ハインリッヒの法則とトライアルの関係
・1539 トライアルの注意点
8/23(金)学習時間:7.25H
・橋本の物理(6)(7)
・CMPプロセスについてまとめ
・4519 建築材料とキャリアとCV
・1826 CV作成に役立つストーリーライティング
コメントを残す